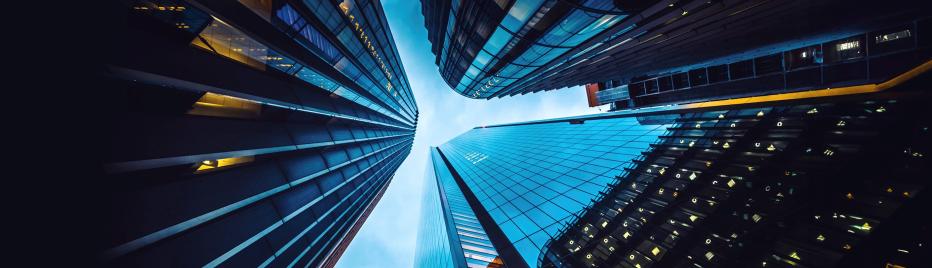
Risks are inherent in any large-scale capital infrastructure program, and in today’s marketplace, the risks have grown exponentially from many perspectives—supply chain, monetary, safety, financing, social value and equity, organization and design and construction to name just a few.
While risk management has been a practice for decades, it is more critical than ever given the complexity of program governance and organizational structures. Regardless of market, infrastructure owners are seeking lessons learned and best practices when it comes to managing, allocating and sharing risks between owners and delivery partners (including contractors, engineers and program managers).
Over my 40-year career, I’ve seen it all on large, complex infrastructure programs across North, South and Central America. I have specialized in leading design and construction of large-scale mega-programs involving challenging schedules; contractual and project phasing elements; proactive risk management; and fast-track methods and multiple delivery systems.
I would like to offer a few insights into how a robust risk management profile that’s actively and continuously managed throughout a program’s life cycle can potentially shave millions of dollars off implementation costs.
My teams take a proactive approach to identifying, minimizing, pricing and mitigating risks and, when we must, effectively responding to risks when they occur. Sound, continuous risk management minimizes project elements from going wrong, reduces impacts if things do go wrong and capitalizes on opportunities to improve project performance and delivery.
In my experience, from California to Colorado to Panama, with side trips to Canada and Arizona, I’ve found that successful mega-programs have three key characteristics:
1. A clear and shared strategic vision.
2. Aligned stakeholders.
3. The ability to quickly adapt and act in complex situations.
So, what are the key risk-related issues that affect all programs? Supply-chain choke points and resource challenges (including inflation); social, community and economic equity initialization and mobilization. Here are some of my top tips on managing these issues in today’s uncertain times.
Understanding supply-chain chokepoints and resource challenges
In competing markets, it is critical to have both local knowledge and global understanding of craft and material resources. My experience has shown me that competition between various projects (whether they are small and local or mega-programs) can exacerbate an already challenging environment. Incorporating adaptability and flexibility with forward planning and purchases helps minimize supply chain and inflationary cost risks, especially over a program’s long timeframe.
However, no matter how much you plan or anticipate, unexpected events such as COVID-19 still happen. It had a massive effect on the global supply chain and ripple effects on the global workforce. It reinforces the need to think creatively when these types of challenges affect the entire industry, with everyone competing for the same (and limited) resources.
Implementing critical social, community and economic equity
A robust and well-planned community, social and economic equity program, developed with community and stakeholders’ input, supplies a secure foundation that creates community goodwill and fosters workforce opportunities. However, its most important benefit is providing those underserved with educational training and employment opportunities (before, during and after construction). A well-planned program also may offer safety, security and access. Without community buy-in, risk issues escalate and an entire program may falter.
Creating robust initiation/mobilization and baselining
Every successful program on which I’ve participated has started with a strong initiation/mobilization plan with a high-level outline of all phases, anticipated program milestones and an initial detailed outline of activities in a program’s early stages, allowing us to “hit the ground running.” Two other factors include developing a program manual and, most critically, getting appropriate buy-in and support from upper management stakeholders.
Risk-related issues, such as supply-chain choke points, interest rate hikes and inflation, and stakeholder buy-in, can lead to programmatic issues. Although we are living in uncertain times, you can use available tools and practices to mitigate or minimize risk, whether you are an owner or delivery partner.
An original version of this article was first published in the Special Advertising section of Engineering News-Record in September 2023.
About the author
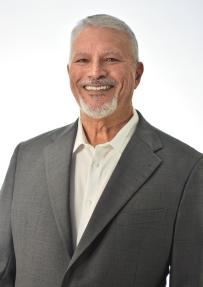
Jacobs Senior Program Manager Joseph (Joe) A. Cazares, PE, specializes in leading design oversight, program management and construction management of large-scale mega-programs involving challenging schedules, contractual and project phasing elements; proactive risk management; and fast-track methods and multiple delivery systems. With a civil engineering degree from UC Berkeley and an MBA with an emphasis on program management and finance from the University of Texas at Dallas, Joe is passing on his knowledge to clients, peers and students. In September 2023 he’s teaching a U of T graduate-level course in project initiation.