Zoetis Expansion Project
Providing speed-to-market through innovative EPCM delivery
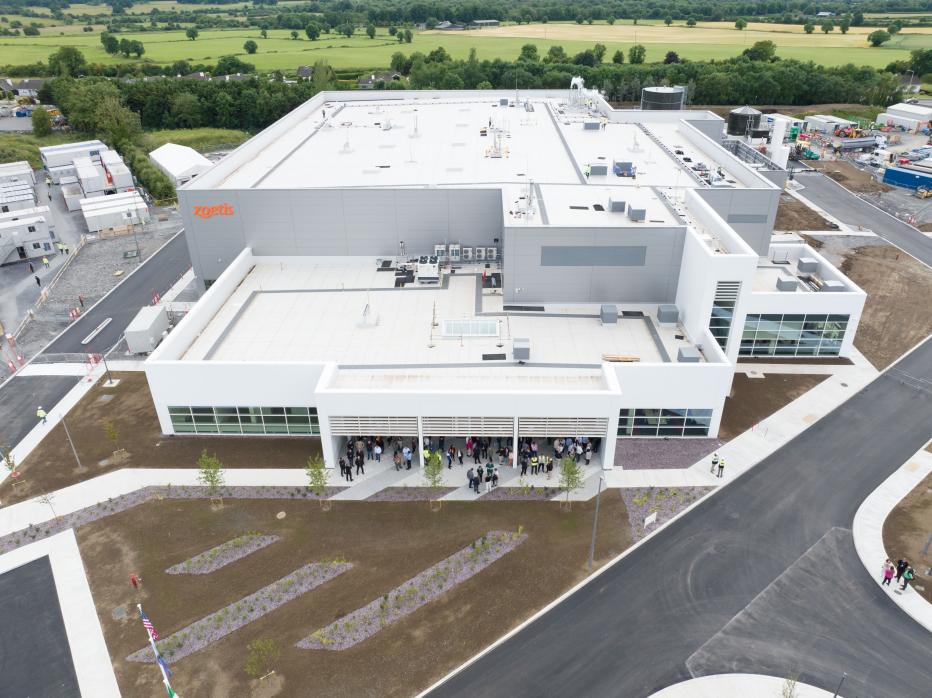
Courtesy of Zoetis
In 2021, Zoetis commissioned an expansion to its biotech manufacturing and development facility in Tullamore, Ireland to increase production capacity for single-use monoclonal antibody (mAbs) for veterinary medicines. As the animal health industry is a cost competitive market, on-time, on-budget quality design and construction was instrumental for Zoetis to achieve an earliest possible product-to-market date. Jacobs was selected to provide engineering, procurement and construction management (EPCM) services for the expansion project, utilizing an Integrated Project Delivery (IPD) model for the greatest schedule savings.
Through the lean-inspired IPD execution approach, Jacobs promoted collaborative behavior between delivery stakeholders and drove greater efficiency, resulting in the project achieving all schedule, quality and cost targets in 23 months.
The Greenfield 8,500 square meter (9,150 squarefeet) facility (and associated ancillary site) site within the Srah Business and Technology Park incorporates functional areas to support production, laboratories, utilities, administration and warehousing spaces. The facility produces Zoetis’ recombinant monoclonal antibodies Solensia and Librela for the animal healthcare market and is now poised to support 80-100 new high-quality jobs in the local economy.
Overcoming challenges…
This highly intricate project necessitated an effective, seamlessly coordinated design delivery approach that drew upon specialized expertise to complete the facility within an accelerated timeline, all while upholding exceptional quality and safety standards.
Schedule: Achieving the earliest possible product-to-market date was a key project driver, spurring a requirement for fast-track project execution with significant overlap between detailed design and construction activities. The typical project delivery duration for advanced manufacturing facilities of this scale ranges from 30 to 36 months; our team completed delivery in 23 months from the start of preliminary engineering to practical completion.
“Right-First-Time” Delivery: Given the schedule imperative and overall competitive nature of the animal health industry, there was minimal tolerance within the project schedule for deviations from plan. A “right first-time” philosophy was critical to maintaining momentum and required our Field Quality Team to work closely with contractors through frequent auditing and weekly quality review meetings.
Flexibility: Zoetis expressed an aspiration that the facility design incorporate flexibility to facilitate the manufacture of other mAbs products in the future.
…for impactful delivery
At the outset, the project applied a collaborative, lean execution approach with early engagement of contractors. Contractor scope incorporated detailed design development, which was managed in a federated model with Jacobs acting as the design integrator.
The open and honest communication ethos promoted on the project from the outset and a “no blame” culture, which set the foundation for boundaryless collaboration between all delivery partners. Once the trade partners were on-boarded, the collective team engaged in multiple Inter-Active Planning (IAP) sessions to align all stakeholders with the project schedule requirements, prioritize design deliverables for construction, and optimize construction activity coordination and sequencing.
Once the team’s foundation was built, a comprehensive range of the latest BIM/Digital technology digital applications were applied to maximize productivity and facilitated collaborative and effective design reviews and clash resolution processes.
As for resulting outcomes due to the foundation of trust on the project:
- Sustainability: The Zoetis building now has excellent energy use profiles that exceed prescribed compliance standards – achieving BER rating of “B1,” which is excellent for the industry. This rating was achieved by close attention to energy efficiency concerns from initial design to on-site installations for building fabric, building services & controls, management and maintenance provisions.
- Safety: A “one-team” safety approach was utilized on the project. To exemplify this, all Environmental Health and Safety (EHS) team members wore PPE labelled “Project Safety” with no company branding. With a TRIR of 0.17, This was an extremely successful project by all safety metrics, and one of the nation’s high-performing projects for 2023.
A significant contribution of the new facility is the creation of high-quality employment opportunities for the Midlands, a region that has been affected by the adverse impact of constraints on Bord na Móna peat production.
The project success was underpinned by the clarity of user requirements; a robust design basis; detailed construction planning; extensive BIM/Digital application; and an exceptional focus on safety during construction.
The project won the Industrial (over €20m) Category of the 2024 Irish Construction Excellence (ICE) Awards and is another great example of the enduring legacy of excellence in the life sciences, semiconductor and critical infrastructure Jacobs has had in Ireland since 1974.
“The newly-constructed facility will utilize cutting edge single use technology which will place it at the forefront of the world’s most advanced biopharma manufacturing site. Jacobs’ great technical diligence and positive focus around safety resulted in an excellent safety record for the project and ensured minimal impact on our neighbors through sensitive design, neighbor engagement and clean non-intrusive construction practices.”
Did you know?
-
23
project schedule (in months)
-
1.2 B+
site work hours (1,212,319)
-
0. 17
total recordable incidient rate (TRIR)
-
16 K
pipework meterage
-
0
environmental events