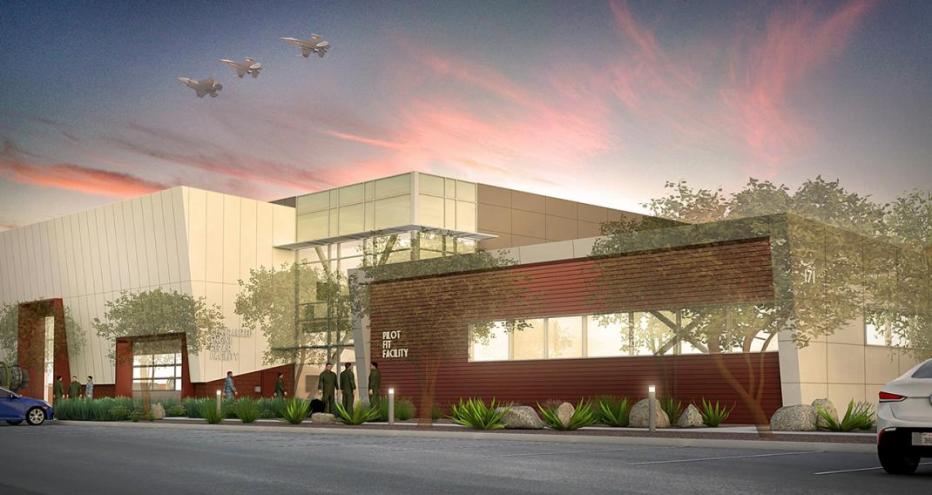
Naval Air Station Lemoore wasn’t a place that stood out for its architecture.
Located in California's Central Valley, this base has far more notoriety as the U.S. Navy's largest strike fighter base and home of the first operational F-35C squadron. The most advanced fighter jets in the world live here, along with all the pilots and maintainers that fly and support them.
The arrival of the F-35, a 5th generation stealth aircraft, required new facilities to support its specialized parts and equipment.
One such effort is the F-35 Centralized Engine Repair Facility & Pilot Fit Facility, which co-locates two core F-35 aircraft functions: a Centralized Engine Repair Facility (CERF) and Pilot Fit Facility (PFF).
The CERF, the first-of-its-kind on the West Coast and second in the entire U.S., supports routine jet engine maintenance and the PFF aids fabrication of specialized flight suits and gear; and custom fabrication and calibration for a computerized F-35 smart helmet.
Partnering with Naval Facilities Engineering Command Southwest (NAVFAC Southwest,) Jacobs provided design, engineering and landscape architecture services to help the facility take flight.
-
27.5 K
square feet (27,553 total)
-
5 th
generation stealth aircraft maintenance and training facility
-
4
maintenance bays
-
1 st
inaugural SAME Design Award winner (2020)
“The overall exterior and interior design, the furniture selections, wall and floor finishes, as well as the color coordination were far superior to most government facilities - which is helping to set the "bar" high for other projects being developed in the area, all while maintaining the government set cost threshold. The A&E Design Team provided exceptional efforts to maximize the efficiencies of the floor plans, which ultimately resulted in cost savings to the Government. Open atmosphere in the design, as well as ganging functions as able, were a few of the tactics proposed and used by the Design Team, which again help in saving the Government money during construction, as well as operational cost savings.”
Project P-380 is a building that pushes the architectural envelope on the Lemoore base. The CERF is the Navy's first standalone F-35 engine maintenance facility, and the PFF is a facility full of high-tech equipment and staff that create the F-35 pilot's flight suits and customized helmets. By co-locating these two programs in the same building and sharing common spaces, we foster interaction among users who are all there in support of one another: the pilots can see the people working in the shop on the engines that will later power their jet, and the maintainers can see the pilots who count on them to keep their jets flight-worthy. This building is designed with passages and portals that physically and visually connect these two groups to bring them full circle in the pursuit of fleet readiness.
The project site was an empty lot in a corner of the base adjacent to one of the runways and surrounded by haphazard building aesthetics, from old concrete test cell monsters to generic metal panel high-bay maintenance boxes to small buildings with glass block windows. These factors let the building approach the site as a blank slate: no dominant styles or materials to dialog with meant we were free to be more architecturally adventurous.
Design Reflects Unique Aircraft and Surroundings
We took advantage of this opportunity to give life and form to the intense dedication and passion the squadron at Lemoore have for their mission: there’s daylighting and vibrant red material accents with human-scale textures throughout the building and the landscaping. We visually expressed the high-tech, stealth capable and supersonic traits of the F-35: there are sleek metal panel canted walls, oblique hallways and view portals framed to mimic the angular surfaces of the F-35.
The building’s exterior architecture is thoughtfully designed to express the F-35 aircraft’s uniqueness, while co-existing harmoniously with its surroundings – including industrial buildings with various architectural themes from different eras.
We designed the building’s interior and exterior to capture the dynamic, modern and high-tech characteristics of the F-35 using a variety of elements, such as the canted metal panel walls, windows and portals that evoke the sleek lines and unique shapes of aircraft and engine nozzle blades. Additionally, we chose colors and textures inspired by the advanced composite materials used in the F-35 aircraft itself.
The PFF wing of the building highlights the modern appearance of the building exterior. The F-35’s revolutionary helmet display feature allows pilots to see through the aircraft and share a common operating picture with squadron mates. These features guide the design of the façade’s transparencies, exposed structure, large curtain walls and sleek metal panel surfaces.
The CERF function also has a significant impact on the building’s exterior design, since this is where the F-35 engine – the beating heart of the aircraft – undergoes routine maintenance. The engine’s distinctive nozzle fin shape inspired the building’s angled walls and window portal designs.
Site Features to Benefit Both Programs
The first floor of the facility provides primary spaces for both functional programs, with the CERF to the east and the PFF to the west. The CERF includes four maintenance bays with associated tool storage; high-density parts storage; racking and crane systems; and pass-through vehicular circulation for engine trailers, forklifts and tugs. Visual connections in and out of the CERF are important, engaging sailors outside with the work performed inside, as well as increasing daylighting and quality of the work environment for maintenance personnel inside.
F-35C pilots in training are measured for flight gear inside the PFF. All flight suits and related gear are personally fitted for each pilot and the helmets are custom-fabricated for fit and calibrated for eyesight. Interior spaces within the PFF include various shops for flight suits and gear tailoring, helmet fabrication, secured storage and offices.
A Slice of History Provides Link to Past and Future
While thinking about designing this building to inspire the next-generation F-35 pilots and maintainers, we were presented with a site opportunity to reflect on the history of all the aircraft and sailors that passed through this base. The original lot contained two concrete pads, the remnants of engine test cell buildings from 1960; these pads were left to weather in the elements and had a deep patina that communicated with long forgotten pilots and maintainers who supported the same mission as those today. We took these pads and broke them into pieces to be placed inside gabion walls for a covered break area, as a reminder that while buildings on most Navy bases may appear architecturally simple, they are still a tangible form to represent the people that give of themselves in defense of our country.
Uncovering the Benefits
The building seamlessly combines the industrial functions of the CERF with the administrative functions of the PFF, unlocking several benefits:
- Sharing common spaces reduces the overall footprint of both facilities, allowing them to be accommodated on the site without disrupting a major utility corridor, minimizing scheduled power potages during construction and significantly reducing construction costs.
- Combining the two programs into a single design and follow-on construction contract saved approximately $4 million in client costs. This approach also achieved significant time savings toward meeting the Initial Operating Capability schedule.
- The square footage saved through shared support spaces allows the building to be more efficient, reducing life-cycle energy and operating costs, and encouraging greater daily interaction between F-35 pilots and the individuals who ensure the performance and safety of their aircraft.
The F-35C Centralized Engine Repair Facility & Pilot Fit Facility received one of eight inaugural 2020 SAME (Society of American Military Engineers) Design Awards, achieving a Merit Award in the Built Project category.