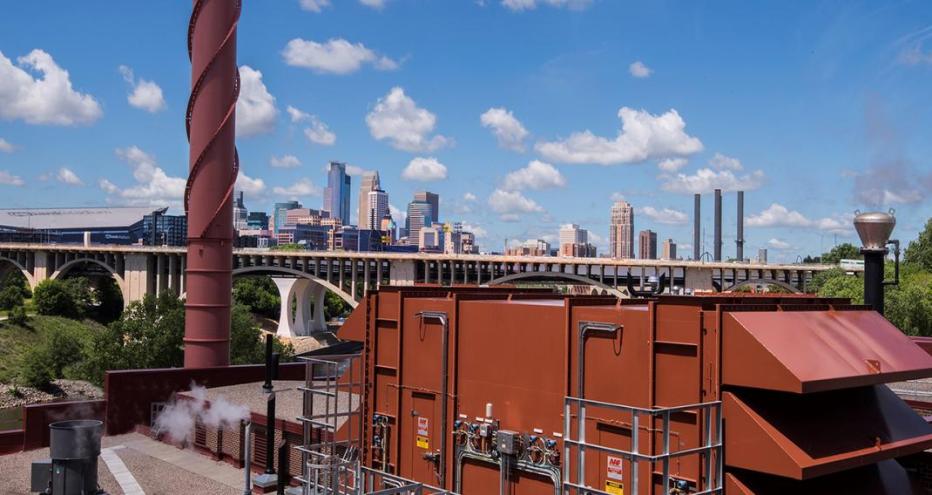
University of Minnesota Combined Heat and Power Plant
We provided holistic engineering services to the University of Minnesota for a new combined heat and power (CHP) plant project to generate power and steam for campus distribution. The facility chose to house the project was the Old Main Heating plant, a 1912-era power plant facility on the banks of the Mississippi River near downtown Minneapolis. It is clearly visible to the public from the Interstate 35 bridge crossing the river. All of the existing boilers were decommissioned in 2000, which was the last time the plant generated steam. Since that time, the facility had fallen into disrepair.
We provided planning, predesign, analysis and equipment optimization, equipment pre-purchase, as-built of existing facilities, design construction administration, and commissioning support services for the decommissioning, historic preservation, and CHP addition to the plant. The upgrade and rehabilitation involved the complete abatement and demolition of seven large coal-fired steam boilers, and subsequently installing a new 22 MW dual-fuel combustion turbine and a 250,000 pounds-per-hour high-temperature heat recovery steam generator which comprised a new efficient and reliable combined heat and power system to provide steam and electricity for the campus.
“The Main Energy Plant marries a historic site and decommissioned plant with world-class technology and environmental stewardship to support the University’s long-term research mission. This is an exciting step that allows us to lessen our carbon footprint while ensuring continuity of operations on campus and saving the University money.”
-
71.5 M
pounds of reduced CO2 emissions annually
-
$ 40 M
in expected lifecycle cost savings over 30 years
-
60 %
or more reduction in consumption of purchased power from the utility grid
-
250 K
pounds-per-hour high heat recovery system
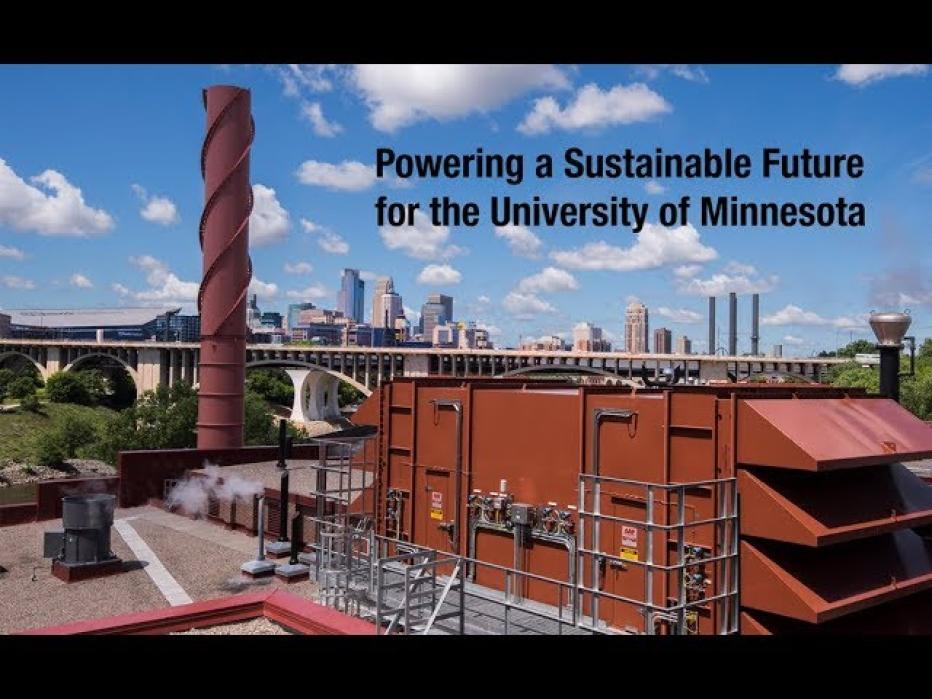
Powering a Sustainable Future for the University of Minnesota
What do you do when you have an energy shortage, a decrepit and contaminated coal-powered steam plant from 1912 that’s built into a bluff of the Mississippi river and an aggressive goal to reduce carbon emissions by 50% by the year 2020?
The answer? Bring in, Jacobs. Partnering closely with the University of Minnesota and its contractors, Jacobs helped convert the plant – named “Old Main” – into a model of modern efficiency and sustainability, resulting in a facility that produces enough electricity and thermal energy to generate all of the University’s steam heat and will save them around $8 million per year in electrical and heating costs.
Key to the success of the project was a complex right-sizing analysis performed by the Jacobs team, which resulted in a revised plant concept costing $1 million more than the original recommendation, but reducing the total anticipated cost of operation, including purchased utilities and maintenance costs, by an additional $98 million during the first 20 years of operation. This wasn’t just a money-saving solution, however: Jacobs also concluded that the optimized equipment would reduce the University’s carbon footprint by an additional 690 million pounds over the 30-year design life of the equipment compared to the original concept, so the benefits to the University’s carbon reduction plan were obvious.
Converting a plant like this required constant innovation to solve the many challenges that arose due to the age of the structure and its location next to the river. Arranging the new equipment into the facility without negatively impacting the 100-year-old structure and surroundings required adopting an equipment configuration normally used in marine applications. Electrical systems were substantially reconfigured across the campus to maximize plant uptime, providing cost savings and improving energy resiliency. Finally, tying into the existing campus heating and power distribution systems required detailed planning and construction phasing plans to maintain continuous operation for the duration of construction.
Now regarded as a beacon of efficiency and sustainability, the new Combined Heat and Power Plant has revolutionized the production of energy on the University of Minnesota’s Minneapolis campus. With the steady operation, the University expects to reduce the consumption of purchased power from the utility grid by more than 60 percent, while also reducing greenhouse gases caused by the consumption of all heat and power on the Minneapolis campus by at least 10 percent, ensuring that the University is well on the way to achieving its carbon emission targets.