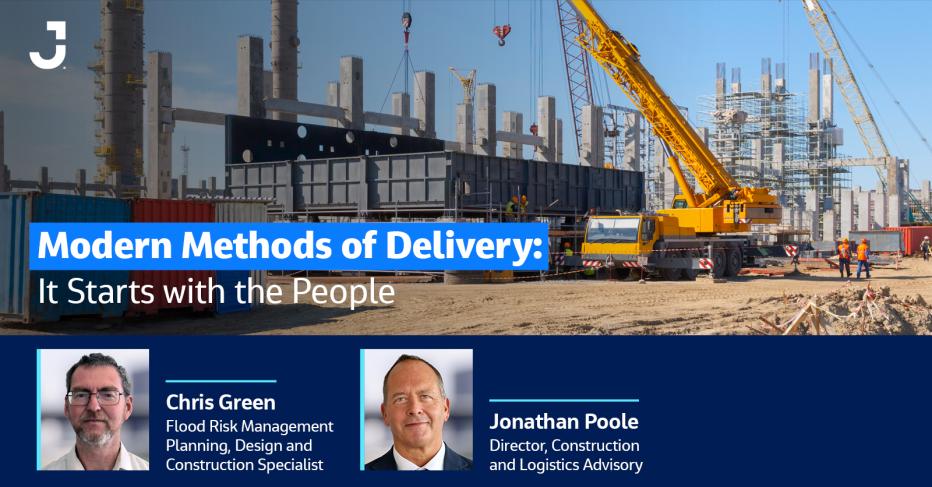
The benefits of Modern Methods of Construction (MMC) are well documented. Global research shows MMC can reduce production time and cost, lower carbon footprints and improve on-site safety and sustainability. A report by the U.K. Commons Housing, Communities and Local Government Select Committee estimated that construction timelines could be reduced by 20–60% using MMC, with a 20–40% cost reduction and lower whole-life costs.
These benefits extend far beyond housing. MMC brings needed innovation to the whole of the U.K.’s construction industry, where productivity challenges, labor shortages and complexity are rising, especially in major infrastructure programs.
Yet despite this promise, successful adoption of MMC remains uneven.
In our experience across sectors, including water, the barriers are typically not technical. They’re human. Based on years of collaboration with clients, supply chains and project stakeholders, we’ve identified four critical insights.
Behavior, not gadgets, is the real challenge
The good news: the technology already exists. MMC has delivered strong outcomes on numerous projects, like using 3D machine guidance at the Black Potts Weir Flood Alleviation Scheme to cut six weeks from the schedule, or GPS-controlled equipment at the Exeter Flood Defence Scheme to enhance construction accuracy and plant safety.
But results can be inconsistent across markets and projects. Two key barriers often appear early: a lack of shared understanding of what MMC means, and incorrect application and measurement of environmental and efficiency performance.
The issue is rarely about tools. It’s about how decisions are made. Clients, contractors and community stakeholders often interpret MMC differently. Aligning everyone’s understanding is essential.
At Jacobs, we define MMC as a set of tools and techniques that boost productivity, reduce risk and increase certainty. It’s not just about drones, 3D printers or robotic equipment. MMC includes new ways of working, digital integration and data-driven decision-making — across the full lifecycle of a project and asset.
This cradle-to-grave approach means building and maintaining durable, multi-purpose assets, like the adaptable flood protection solutions in TEAM2100. These use digital asset management with CAD model data embedded in object requirement systems. Even in highly bespoke environments like flood defense, some components (e.g., pumping stations, weirs, floodgates) can be standardized for off-site production and reuse.
A standout example: the lock gates at Sunbury Dry Dock, part of the Thames Weirs program. Made with fiber-reinforced polymer instead of steel, they have a projected 100-year lifespan, need little maintenance and reduce carbon by 37%.
Front-end loading: Plan early, succeed later
Understanding what’s needed, and how MMC can deliver, starts early. Our Construction & Logistics Advisory team applies Front-End Loading (FEL), an approach that invests in early risk mitigation, stakeholder engagement and informed decision-making.
FEL includes Virtual Design and Construction (VDC), a 3D and 4D planning approach that improves client understanding, solves logistical challenges and enhances communication before work begins. For example, using a 3D viewer to preview lock upgrades in Teddington helped align stakeholders. In another case at Tilbury Docks Lock Replacement, VDC modelling was used to visualize the removal and installation of the two new pairs of lock gates in an operational port. The visualizations were initially used to plan the works, identify clashes and verify the design. Appropriate installation methodologies were then added, ratified and then optimized to minimize marine plant requirements and reduce costs. Digital rehearsals were undertaken to provide construction assurance and ensure optimal safety for all stakeholders in this constrained and busy operational environment.
These “virtual rehearsals” show how talent and technology, aligned early, can drive collaboration and lead to better outcomes.
Access and customization matter
MMC methods like Design for Manufacture and Assembly (DfMA) and Off-site Manufacturing can reduce labor needs, improve safety and durability, and cut carbon emissions. We’ve been applying these techniques for years.
Still, practical constraints matter. Off-site production works best when sites have road access for large equipment. This is often not the case for assets like flood defenses, where ground conditions and environmental constraints such as vegetation make logistics harder.
Another challenge: standardization. Pre-cast components must account for worst-case scenarios. That can mean overdesigning products to suit variable conditions, which increases cost, carbon and time. In some cases, on-site solutions are better. For instance, ground bearing concrete slabs are efficiently placed by pouring concrete in place which bonds to the uneven ground. It negates the need for complex alternative pre-cast alternatives that require significant ground preparation, careful tolerance control, complex joints between adjacent pre-cast components, cranage and typically an in situ concrete stitch. Our experience in the application of Eurocode 7 on the Exeter Flood Defence Scheme shows that pre-cast slabs need to be built up to 30% larger than in-situ slabs to achieve the required sliding resistance to flood loads.
Successful application relies on experience and education. And while OSM is already widespread, it’s often underrecognized or measured in the wrong way.
Measure what matters, not what’s easy
MMC is often linked to innovation and sustainability, but without a shared measurement framework, this can turn into vague goals and unmet expectations. Some specifications demand innovation from suppliers but penalize teams when results are not delivered as promised.
The solution: incentivize the right behaviors. Don’t reward innovation for its own sake. Instead, align metrics to meaningful outcomes.
Pre-Manufactured Value (PMV) is the most common MMC metric, measuring the proportion of a project’s cost spent on pre-manufactured components. But PMV alone doesn’t capture whether a project met budget, stayed safe or cut carbon. It doesn’t reflect delivery success.
On a recent project for a major airport market leader, we shifted the focus away from the conventional 50% Pre-Manufactured Value (PMV) target, a widely used industry benchmark for OSM. We recognize that while it can be useful, it often overlooks broader and more critical factors of program and project delivery. These include schedule reliability, cost certainty, operational safety, risk mitigation, logistics complexity, temporary works and construction-related carbon impacts.
Instead, we introduced custom metrics aligned with the client’s strategic objectives. These metrics evaluated the assets lifespan, with a particular emphasis on extending lifespan, supporting the client’s long-term growth strategy and reducing environmental impact. This approach enabled cost efficiencies through the ability to repurpose and standardize components across a diverse infrastructure portfolio.
We also used data to make decisions within a VDC environment, allowing digital rehearsals to minimize disruption and maintain safe continuous operations for customers. Ultimately, this performance-led approach reinforced the alignment with the organization's vision for sustainable infrastructure, its corporate growth ambitions and its commitment to delivering greater value through innovation, resilience and productivity.
From MMC to modern methods of delivery
True innovation isn’t about flashy tools. It’s about applying the right processes, with the right people, inside a framework that promotes continuous learning. That means starting with front-end loading to develop a robust and credible construction strategy, using collaborative contracts, involving the supply chain early, adopting a design–to–build mindset and tracking purpose-built metrics that reflect real project performance.
About the authors
Chris Green, Flood Risk Management Planning, Design and Construction Specialist
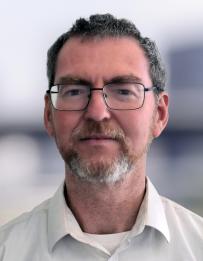
Specialist in flood risk management planning, design and construction. Chris focuses on protecting communities, managing construction risk and advancing sustainable, river-sensitive development through deeper client collaboration.
Jonathan Poole, Director, Construction and Logistics Advisory
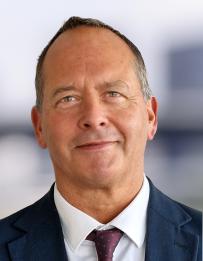
Chartered civil engineer with more than 36 years of delivery experience across heavy civils, aviation, highways and rail. As Director of Construction and Logistics Advisory, Jonathan leads a team of 64 professionals to embed early construction guidance into design, ensuring risk-managed, efficient outcomes.