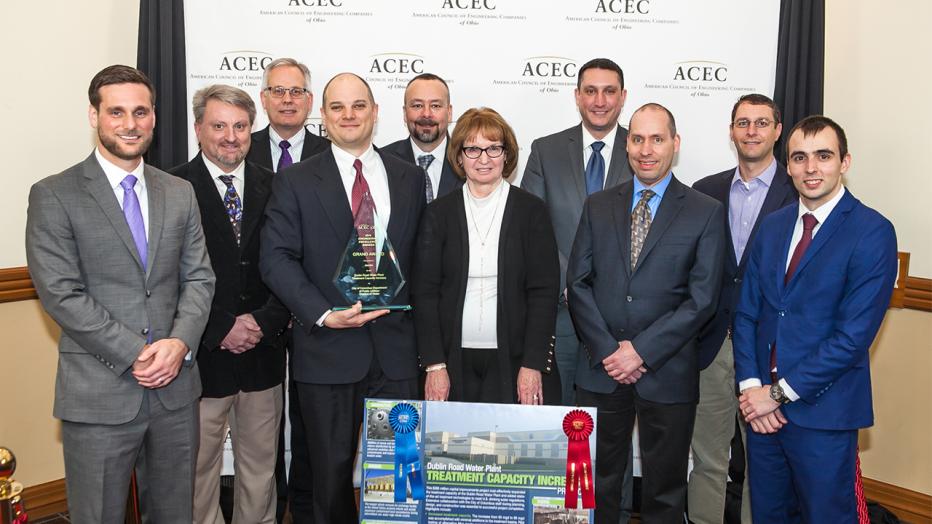
Faced with potential regulatory exceedances, seasonal taste and odor issues, aging infrastructure and increasing water demands, the City of Columbus Department of Public Utilities (DPU) contracted Jacobs to select treatment technologies that would meet drinking water regulations and increase overall water treatment plant reliability.
The $285 million capital improvements project at the Columbus, Ohio Dublin Road Water Plant (DRWP) expanded the treatment capacity and added state-of-the-art treatment technologies (ozone, filtration with BAC and ion exchange) to meet U.S. drinking water regulations. The upgrades also provide DPU with increased reliability and barriers against future potential regulatory concerns. Extensive collaboration with DPU staff during planning, design and construction was essential to successful project completion.
Completed in 2018, the DRWP improvements resulted in the largest nitrate removal ion exchange facility in the nation and the first ozone and biologically active filter treatment combination to be commissioned in Ohio. In recognition of project success and technical accomplishments, the Jacobs project team recently received the Grand Award at the American Council of Engineering Companies (ACEC) of Ohio’s 2019 Engineering Excellence Awards.
Treatment capacity increase project has multiple objectives
Increased treatment capacity; increased consumer safety; reduced operating costs; and reduced capital expenditures – these objectives all factored into the DRWP Treatment Capacity Increase Project, in addition to DPU’s wish to embrace sustainable design, construction and operations throughout the project.
What would become one of the DPU’s largest infrastructure upgrade projects began in 2010, when the Jacobs project team led a blue-ribbon panel of Columbus staff and industry experts to evaluate treatment alternatives to meet the DPU’s challenges. The panel selected improvements that resulted in approximately $100 million in construction cost savings, addressing the client’s objective of reducing capital expenditures. The final project cost of $277 million was below the budget of $285 million.
The increased treatment capacity (from 65 to 80 million gallons per day (mgd) was accomplished with minimal additions to the treatment basins. Pilot testing of alternative filter media supported increased filter capacity without construction of new filters. The selected treatment improvements include:
- Combining ozone addition and biological filtration to reduce levels of disinfection-by-products (DBPs) in the treated water.
- Ion exchange treatment to remove nitrate from the raw water.
- Ozone addition to improve taste and odor of the treated water.
The innovative addition of ion exchange, ozone, biological filtration and advanced oxidation increased treatment capabilities and reduced potential impacts to public health by lowering nitrate levels and DBPs to increase consumer safety.
Core features of the design included energy efficiency and reduced operating costs. Retrofits to finished water pumping systems reduced annual energy costs by 11%, while adding ozone eliminated powder activated carbon treatment reduced annual operating costs by $700,000. The biological filter runtime is greater than anticipated, further decreasing operational impacts, and reduced chlorine demand increases operational savings even more. The recarbonation system has also proved to be more reliable than anticipated, also reducing operational impacts.
Sustainable construction and energy efficiency
The DPU requested that sustainable construction and operations be a core value for the project. The project team incorporated environmental design features such as porous paving, bioretention ponds, reflective roofing and building ventilation controls, all of which will support DPU’s application for LEED Silver Certification for the facility.
By upgrading equipment at or near the end of its useful life, the project addressed aging infrastructure concerns and achieved greater energy efficiencies. Significant improvements included a new electrical substation; upgraded plant electrical systems; a new residuals pump station; a new recycled filter backwash water system; chemical systems improvements; high efficiency finished water pumps and HVAC improvements; and sustainable stormwater facilities.
Complex, multi-contract construction
The project was divided into five construction contracts to sequence improvements on the space restricted site while continually providing safe and reliable drinking water to the roughly 400,000 consumers during the 6-year construction period (2012 to 2018).
The DRWP upgrades provide our client and their customers with increased reliability, regulation compliance and barriers for future potential regulatory concerns. The sustainable improvements provide the foundation for an improved method of treating water for generations to come.
Client satisfaction through technical innovation and relationships
Complimenting the project team, involved from initiation to conclusion, Project Manager Matt Leach said, “Completion of this project is a testament to all the hard work of the team – client, staff and subconsultants. A project of this size and complexity required a lot of hard work and coordination with the client and our project team.”
“The City of Columbus demonstrated their commitment to providing safe and reliable drinking water to the community, and our team was committed to making the project a success,” he added.
-
The largest nitrate removal ion exchange facility in the U.S. protects infants and avoids maximum contaminant level exceedances during intermittent raw water high nitrate events.
-
A rooftop rain garden and other sustainable features were implemented to support future application for LEED Silver certification.