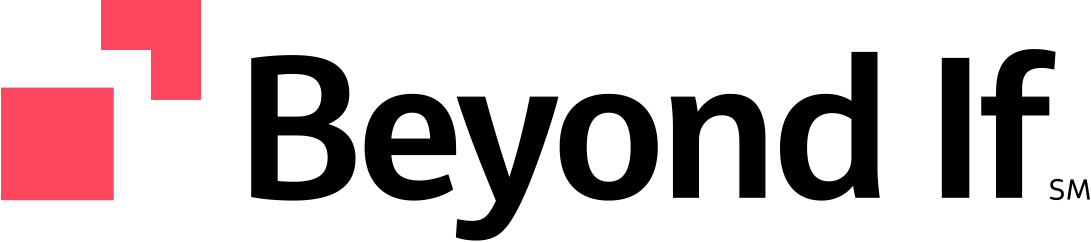
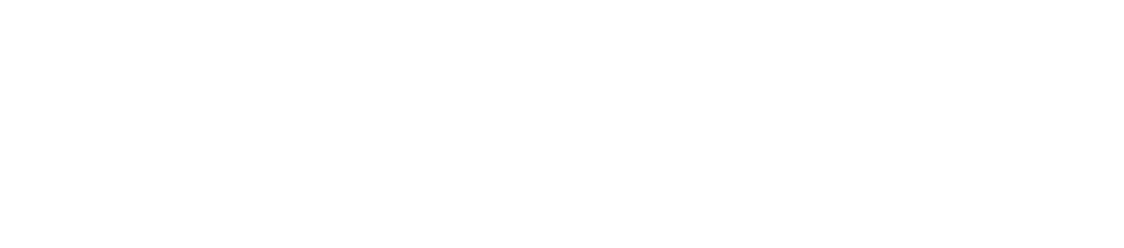
For more than 30 years, Jacobs has been responsible for planning and implementing Lead and Copper Rule-related strategies which protect millions of people in the U.S. and Canada. Our work includes enhanced water quality monitoring strategies, sampling plan development, harvested pipe-scale analysis, lead service line inventories and replacement plans, corrosion control studies and the incorporation of equity and environmental justice considerations into compliance programs.
A curated selection of some of the top-listened to and trending podcast episodes from our popular If/When podcast series.
Jacobs. A world where you can.
As a purpose-led company, we know we have a pivotal role to play in addressing the climate emergency. We consider this not only good business, but our duty to channel our technology-enabled expertise and capabilities toward benefitting people and the planet.
We work in partnership, delivering some of the most challenging, diverse and innovative projects and programs globally across multiple sectors. We integrate complex interfaces across planning, procurement and delivery to help unlock better social, environmental and economic outcomes from mega and giga projects.
As our clients navigate the digital transformation and growing cyber risks, we have positioned ourselves at the forefront of this growth, adding digital capabilities, products and tools to serve a growing set of customers.
Sit down with our visionary team of thinkers, dreamers and doers to see what a day in the life is like.
Together with our visionary partner, PA Consulting, we're establishing our position in high end advisory services, creating a springboard to expand in high value offerings beyond the core.
At Jacobs, we're challenging today to reinvent tomorrow by solving the world's most critical problems for thriving cities, resilient environments, mission-critical outcomes, operational advancement, scientific discovery and cutting-edge manufacturing, turning abstract ideas into realities that transform the world for good. With approximately $16 billion in annual revenue and a talent force of more than 60,000, Jacobs provides a full spectrum of professional services including consulting, technical, scientific and project delivery for the government and private sector.
As climate change threatens water security around the world, more communities are turning to water reuse as a resilient water supply solution and embracing the OneWater principle that all water has value. Jacobs has been supporting clients with water reuse programs for decades, beginning with the first applications of advanced wastewater treatment technologies in the 1960s. We provide our clients with a full range of services, from water reuse feasibility studies to design, construction and operations.
The only certainty about the future is uncertainty. Resilience is an attribute of a smarter planet, and requires planning and adapting ahead of potential threats. We help our clients survive, recover, adapt and thrive.
Jacobs is working to help clients across the United States secure federal funding for projects that make our cities and communities more connected and sustainable. Working hand-in-hand with clients from coast to coast and everywhere in between, Jacobs develops bold, innovative solutions to address the nation’s toughest challenges.
Now more than ever, we appreciate the hard work, sacrifice and dedication of the medical profession in ensuring the health and safety of our communities.
Together, we are stronger. Together, we can transform the future.
We’ve provided design-build services to the water sector for over 25 years and delivered more than 150 projects. We offer fully integrated design-build and design-build-operate capabilities to tackle the most complex water challenges and work in close collaboration with our clients.
Stories that capture our partnerships and innovative impact for a more connected, sustainable world
As the world prepared for the Year 2000, stocking up on everything from water and non-perishable food items to cash and radio batteries, Spokane County in Washington State was beginning plans of its own.
Spokane County decided in 1999 – for several reasons, including meeting future population growth, eliminating septic tank service, achieving lasting cost benefits and reducing phosphorous discharge to the Spokane River – that the time had come to invest in their future by building a new greenfield plant. So, they started planning for a new facility plant and partnered with Jacobs in 2009 to design, construct and operate it.
Since nutrients – such as phosphorus or ammonia – in wastewater contribute to algae growth and reduced oxygen in local waterways, removing nutrients was a critical path of the treatment process design for the new Spokane County Regional Water Reclamation Facility (SCRWRF). In fact, the new facility was challenged to meet some of the most stringent permit limits for phosphorus of any treatment plant in the U.S., aiming to protect both the Spokane River and Lake Spokane.
But what if we showed you how the facility became the first to use process simulation, using Jacobs’ Replica™ digital twins solutions software to design a greenfield, state-of-the art, ultra-low phosphorus membrane bioreactor (MBR) system that’s ultimately removing over 99.9% of the phosphorus in its effluent?
successful Replica Process project applications around the globe
removal in phosphorus in effluent (<0.05 mg/L TP) – powered by first use of process simulation to design an ultra-low phosphorus MBR system
“Jacobs’ Replica Process whole plant simulation platform was put to the test on the SCRWRF DBO project. It showed that simulation can safely and reliably be used to design and evaluate first-of-their-kind technologies under the most stringent compliance conditions.”
Bruce Johnson
SCRWRF Lead Process Designer and former Jacobs Global Wastewater Process Simulation Technology Leader
Wastewater process models can be as simple as a representation of the power usage of a pump or as complex as computational fluid dynamics activated sludge or biofilm system. They consist of many mathematical equations that describe reactions and reaction rates of biological, chemical and physical phenomena of various unit processes, and their accuracy varies upon what is being modeled and the sophistication of the model.
That might sound complex, but wastewater process models are actually powered by math you can do by hand. However, computers of course can do it much faster and when utilities today are constantly doing more with less, these quick, reliable results bring undeniable benefit throughout the project lifecycle.
During the process design phase on the SCRWRF, our team relied on a plant-wide process model, generated using Jacobs’ Replica Process™ simulation platform, formerly Pro2D2™, integrated with Replica Parametric Design™ to make decisions between using MBR or tertiary membranes and whether to use biological, chemical, or biological and chemical phosphorus removal techniques.
Replica Process is a whole-plant simulator that tracks dozens of different wastewater components throughout each unit process, providing the capability to integrate process and design information to evaluate existing systems or size new ones. Since membranes were mandated for the SCRWRF, our team used the simulation to work through a range of considerations including unknown influent characteristics, the need for high confidence in achieving very low phosphorus limits (< 0.05 mg P/L), balancing the needs of phosphorus removal with nitrification and total nitrogen removal requirements, lowering capital and operating costs and minimizing operational risk.
We ultimately elected to use MBR technology with chemical enhancement at SCRWRF. This treatment process has six-million individual membrane fibers that filter out nearly all the suspended solids in the wastewater. These solids are then stabilized and treated, before being trucked to a composting facility where they become a fertilizer product.
At this greenfield facility startup in 2011, the county hit the ground running – starting up at more than 80% of the design capacity of approximately 8-million gallons per day of sewage from the city’s existing treatment facility and ultimately removing approximately 25 pounds per day of phosphorus loading that would otherwise go to the Spokane River. This together with the low phosphorus limits (< 0.05 mg P/L), marked an outstanding achievement at startup.
Not only is the SCRWRF the first greenfield facility to have used process simulation to design an ultra-low phosphorus MBR system, it’s also the first to use process simulation to model the performance of aerobic digestion after anaerobic. Now, our operations team at Spokane use Replica Process for monitoring, to influence operational plans and to complete various scenarios in advance of future compliance requirements.
Today, the county continues considering opportunities to beneficially reuse SCRWRF’s Class A reclaimed water for industrial uses, urban irrigation and wetlands restoration. Reuse of water is important because it benefits the Spokane Valley Aquifer by reducing the amount of water that must be withdrawn to meet regional water demands and can also enhance low flows in the Spokane River, since much of the water in certain reaches of the Spokane River during the summer months is from the aquifer.
The plant serves as a catalyst for revitalization of the area, while being a good neighbor to existing developments. We implemented an advanced SCADA system that can allow unattended operations and integrated it with maintenance management and operations optimization programs to minimize operation and maintenance costs. Additionally, SCRWRF’s cogeneration system – which captures biogas from the anaerobic digesters, stores it and then transfers it to a gas conditioning/micro-turbine system that generates electricity and hot water for process and utility needs.
These benefits helped the facility earn the 2013 Washington Industrial Energy Leaders Award and because the project used design-build delivery, designers worked closely with the construction team to consider energy and life-cycle costs of the facilities and implement solutions that provided these energy and electricity savings.
Not only is this renewable energy helping the environment and reducing electrical costs, we also designed several features to meet LEED™ Silver criteria. Our team ultimately self-performed all design disciplines for the LEED™ Silver‐certified Water Resource Center, Treatment Operations Facility and Maintenance Buildings; including mechanical, electrical, structural, civil, instrumentation and controls (I&C), heating, ventilation and air conditioning (HVAC), architectural, geotechnical and process. We also led permitting, construction management, yard piping, equipment installation, process mechanical, concrete/civil work, SCADA and I&C installation and long-term O&M operations and planning.
The Design-Build Institute of America gave the SCRWRF its National Award in 2012, recognizing the team’s excellent, integrated approach to deliver design and construction services under one contract with a single point of responsibility.