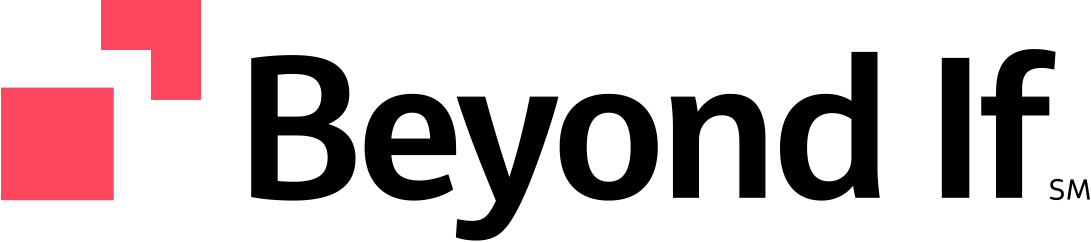
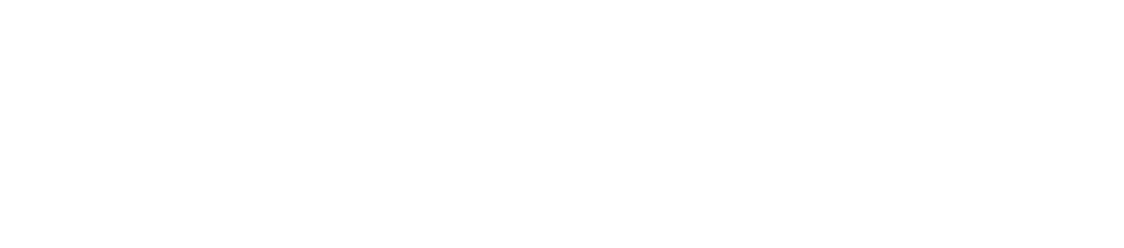
For more than 30 years, Jacobs has been responsible for planning and implementing Lead and Copper Rule-related strategies which protect millions of people in the U.S. and Canada. Our work includes enhanced water quality monitoring strategies, sampling plan development, harvested pipe-scale analysis, lead service line inventories and replacement plans, corrosion control studies and the incorporation of equity and environmental justice considerations into compliance programs.
A curated selection of some of the top-listened to and trending podcast episodes from our popular If/When podcast series.
Jacobs. A world where you can.
As a purpose-led company, we know we have a pivotal role to play in addressing the climate emergency. We consider this not only good business, but our duty to channel our technology-enabled expertise and capabilities toward benefitting people and the planet.
We work in partnership, delivering some of the most challenging, diverse and innovative projects and programs globally across multiple sectors. We integrate complex interfaces across planning, procurement and delivery to help unlock better social, environmental and economic outcomes from mega and giga projects.
As our clients navigate the digital transformation and growing cyber risks, we have positioned ourselves at the forefront of this growth, adding digital capabilities, products and tools to serve a growing set of customers.
Sit down with our visionary team of thinkers, dreamers and doers to see what a day in the life is like.
Together with our visionary partner, PA Consulting, we're establishing our position in high end advisory services, creating a springboard to expand in high value offerings beyond the core.
At Jacobs, we're challenging today to reinvent tomorrow by solving the world's most critical problems for thriving cities, resilient environments, mission-critical outcomes, operational advancement, scientific discovery and cutting-edge manufacturing, turning abstract ideas into realities that transform the world for good. With approximately $16 billion in annual revenue and a talent force of more than 60,000, Jacobs provides a full spectrum of professional services including consulting, technical, scientific and project delivery for the government and private sector.
As climate change threatens water security around the world, more communities are turning to water reuse as a resilient water supply solution and embracing the OneWater principle that all water has value. Jacobs has been supporting clients with water reuse programs for decades, beginning with the first applications of advanced wastewater treatment technologies in the 1960s. We provide our clients with a full range of services, from water reuse feasibility studies to design, construction and operations.
The only certainty about the future is uncertainty. Resilience is an attribute of a smarter planet, and requires planning and adapting ahead of potential threats. We help our clients survive, recover, adapt and thrive.
Jacobs is working to help clients across the United States secure federal funding for projects that make our cities and communities more connected and sustainable. Working hand-in-hand with clients from coast to coast and everywhere in between, Jacobs develops bold, innovative solutions to address the nation’s toughest challenges.
Now more than ever, we appreciate the hard work, sacrifice and dedication of the medical profession in ensuring the health and safety of our communities.
Together, we are stronger. Together, we can transform the future.
We’ve provided design-build services to the water sector for over 25 years and delivered more than 150 projects. We offer fully integrated design-build and design-build-operate capabilities to tackle the most complex water challenges and work in close collaboration with our clients.
Stories that capture our partnerships and innovative impact for a more connected, sustainable world
It’s been 48 years since David Bowie’s hit song, “Life on Mars” hit the airwaves, but the question in its chorus, ‘Is there life on Mars?’ remains a pop culture and scientific phenomenon.
Supporting future exploration of Mars, its past and other far out locations in space depends on designing and constructing habitable places for astronauts to live and work on the surface. On Earth, the demands placed on our housing and infrastructure are fast outstripping capacity as populations surge. Estimates from McKinsey Global Institute project that by 2025, around 1.6 billion people living in cities might struggle to secure decent housing.
But what if we showed you how Jacobs and NASA scientists are exploring planetary habitat manufacturing and assembly technologies, such as 3D printing, to develop options for practical, affordable and flexible structures capable of thriving whether on land or in space?
estimated savings in material launched from Earth
day of construction vs. the traditional 5
“Being able to 3D print whatever structures or parts we need on-demand, using feedstock made from in-situ resources, will enable us to be independent of Earth, in that we could grow our own surface infrastructure and create our own spare parts as needed. Additionally, whatever we can produce on a planetary surface will not need to be sent from Earth and will save the time and cost of launching those materials – a gamechanger for NASA.”
Jennifer Edmunson
Jacobs Geologist and In-Space Manufacturing Engineer
A one-way trip to Mars would take astronauts anywhere from six to nine months and once they arrived, there would need to be habitable places for them to stay. Given the time it takes to get to Mars, and that a trip to a store for supplies isn’t something the astronauts can add to their to-do lists once in space, 3D printing is exploring options previously conceived impossible.
To get ready for the building of roads, berms and structures on the planet, Jacobs and members of the In-Space Manufacturing team at NASA’s George C. Marshall Space Flight Center (MSFC) in Huntsville, Alabama are experimenting with 3D printers and the benefits afforded by them for a process called additive construction.
Like other additive processes, additive construction starts with turning a computerized geometric model of a part into a set of printing instructions for a 3D printer. Then, the structure is printed, layer by layer, using the defined coordinates and printing parameters.
When it comes to designing these structures, one of our team’s first and primary tasks is studying the planet’s soil chemistry, mineralogy and geomechanical properties – key to developing construction materials, from the in-situ resources, that can withstand Mars’ cold, airless and rusty desert surface. These studies will help produce designs for structures capable of providing radiation and ballistic protection and maximize structural support despite low-pressure environments.
3D-printing infrastructure and use of local materials for construction is estimated to reduce the amount of materials transported from Earth by 60 to 90 percent, significantly reducing construction costs and time and even reducing the environmental impact by using less material and generating less waste. The team already found success using a Martian simulant to create cement construction material and they are hopeful that one day, after more research into strength, oxidation barriers, radiation shielding potential and more, they’ll be able to use 3D printing technology to fabricate an entire outpost.
While the thought of 3D printing infrastructure on the Red Planet is extraordinarily cool, additive construction technology’s origins are a bit more grounded. Jacobs is even assisting as the technology moves into other markets, such as military applications and state and local governments.
For broader society the potential to harness additive construction to solve looming problems on Earth, such as the housing crisis, is particularly exciting. Nearly 30 million U.S. households face one or more of the following issues: cost burdens, overcrowding and space inadequacy. Worldwide, while large cities in developing countries have been growing at rates nearing five percent per year, slums and squatter settlements have been growing nearly twice as fast.
Additive construction is adaptable, on-demand and can be used in a variety of settings. The technology allows simple military base housing to be built in just one day, instead of the typical five. Currently homes in the U.S. take more than half a year to construct. 3D printing is more cost economical, using just half the material used for typical builds; and it also requires fewer personnel – which could free up more time to build additional structures to help bridge the housing gap.
Recently, members of NASA’s MSFC In-Space Manufacturing team, supported by Jacobs, developed a full-scale additive construction system for the U.S. Army Corps of Engineers (COE) Research Laboratory in Champaign, Ill. The COE and the U.S. state of Hawaii are interested in using the technology to minimize the need for materials to be imported from the mainland. Imagine what the technology could accomplish in confronting the issues facing the U.S.’s traditional infrastructure such as roadways and water systems.