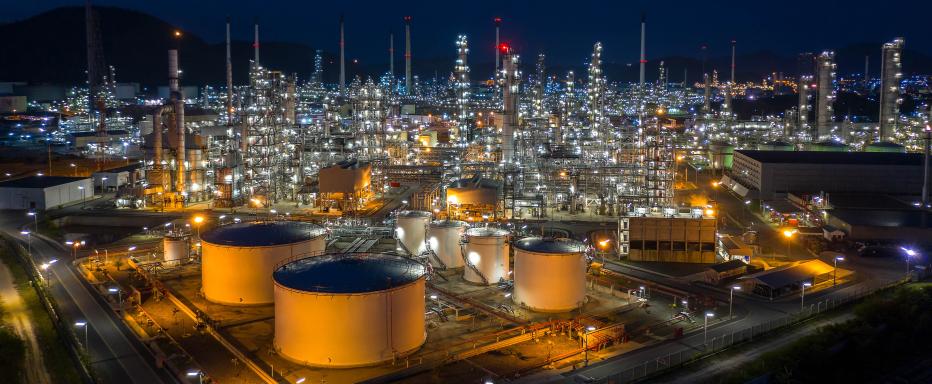
Our solutions include:
Applying big data analytics and internet of things technologies
Smart asset managers and facility planners focus on the total cost of ownership Total Cost of Ownership (TCO) of their facilities and infrastructure. For new capital projects, designers often seek to lower TCO through innovative use of new technologies or sustainable building approaches. However, even in those cases, approximately 75% of TCO is locked in the operations and maintenance of the facility infrastructure and systems after commissioning. That number is even higher for organizations that desire to extend the service life of their infrastructure, balancing the risk of reduced reliability for the payoff of more productivity out of their fixed and aging infrastructure.
Whether considering new infrastructure or trying to extend the life of existing infrastructure, reducing TCO requires an innovative asset management solution that leverages new technologies and big data analytics to optimize and enable proactive maintenance approaches. Our solutions are proven to reduce TCO by up to 40%.
Internet of Things (IoT) solutions for asset management
Jacobs applied IoT solutions long before IoT became the catch phrase it is today. As far back as the 1990s, we were instrumenting HVAC systems, rotating turbomachinery, and other infrastructure with accelerometers, temperature sensors, strain gauges and other sensors to assess system performance. By analyzing the collected data, we’ve established algorithms and criteria that allow early detection of equipment anomalies that can be corrected long before that equipment fails and impacts facility availability.
Today, Jacobs employs the latest versions of wireless asset Predictive Maintenance (PdM) devices to auto-monitor the health of critical assets and perform self-analytical diagnostics in real-time. Remote monitoring allows us to make real-time, informed business decisions as to when asset components need replacing, repairing or recalling, and whether they are maintainable or approaching the end of their life cycle.
Preventive maintenance optimization
Performing too much Preventive Maintenance (PM) creates costs in that it is wasteful on resources that could be better spent on assets that are experiencing failures. Not only are the direct costs of labor, materials, equipment, and planned downtime the results of unnecessary PM, but some PM tasks disrupt complex systems in a way that engenders further costs.
To combat these challenges, we’re equipped to perform PM Optimization activities to help ensure that its PM program is as efficient and effective as possible as tailored to each client. PM Optimization is a structured process using Reliability Centered Maintenance (RCM) principles and involving our certified maintenance and reliability professionals and technicians to mitigate operational risks, improve operational performance and eliminate unnecessary, redundant and ineffective PMs.
Whole life asset management
We deliver a full suite of tailored operations, maintenance and facility-management solutions that enable critical missions. Our services cover the entire asset lifecycle and drawing on a wide range of experiences from global government and commercial markets, we offer the best value for managing and maintaining the assets that you own and operate. With Jacobs as your partner, you have access to local knowledge plus a world of technical ability from engineers, project managers and related experts throughout our global team of more than 55,000 visionaries, dreamers and doers.
Reliability-Centered Maintenance (RCM) and Condition-Based Maintenance (CBM)
Our IoT solutions enable effective RCM and CBM approaches. Incorporating the Society for Maintenance and Reliability Professionals’ (SMRP) Five Pillars of Knowledge, ISO 55000 principles and our maintenance best practices, our RCM and CBM approaches combine a deep understanding of the assets we maintain, their condition, and their mission criticality. By identifying and focusing on critical systems, performing analyses to identify bad actors and/or highest maintenance cost systems, and implementing analysis recommendations and follow-up monitoring, we ensure the desired improvements and benefits are realized.
Jacobs’ innovative Condition Based Maintenance (CBM) approaches use manual and remote monitoring to determine real-time asset health. We’ve developed our AM solutions using both perspectives, fusing the insights from each to yield more effective solutions. Not only do we perform both types of services, but we let our daily maintenance perspective inform our solution architects. While we have success stories when we are allowed to perform in only one of those domains, our most impactful success comes when we have an opportunity to integrate our engineering/analytical approaches with our daily maintenance expertise.
Asset Management Solutions Handout
Applying big data analytics and IoT to reduce cost of ownership
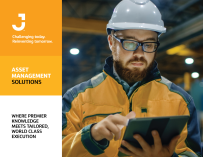
Traditional facility operations and maintenance approaches focus on accomplishing prescriptive maintenance activities at periodic intervals based upon designer or manufacturer recommendations. These approaches are usually reactive as technicians respond to failed systems to restore functionality. Over time, daily facility availability becomes unpredictable. To avoid such reactive maintenance, Jacobs AM solutions focus on predictive analytics and real-time system/subsystem condition assessments to optimize your preventive maintenance program in a proactive manner.